Planung und Fertigung innovativer Faserverbundsysteme
Faserverbundsysteme ermöglichen futuristische Designs und bieten Potenziale im Bereich der Nachhaltigkeit. Eine individuelle Faserorientierung sowie die Entwicklung von entsprechenden Laminaten ist mit einem herkömmlichen, linearen Planungsprozess und konventionellen Produktionstechnologien jedoch kaum umsetzbar. Um die Anforderungen aus Architektur, Tragwerk und robotischer Fertigung in einem kontinuierlichen digitalen Prozess zu integrieren, wurde ein neuartiger Co-Design-Ansatz entwickelt [BUGA Faserpavillon 2019]. Auf diese Weise können Dichte und Ausrichtung der Fasern von Architekt*innen und Bauplaner*innen in jedem Bauteil unter Berücksichtigung der Fertigungsbedingungen individuell abgestimmt, strukturell ausgelegt und architektonisch gegliedert werden.
Das bietet WiTra zu Planung und Fertigung innovativer Faserverbundsysteme:
- Durch Co-Design-Ansätze die Nachhaltigkeit von Faserverbundsystemen erhöhen? Lernen Sie, was hinter Co-Design-Ansätzen steckt. Erfahren Sie zudem wie sie Architekt*innen und Bauplaner*innen bei der Gestaltung innovativer und nachhaltiger Konstruktionen auf Basis von Faserverbundsystemen unterstützen können. Direkt zu
- Was sind die Nachhaltigkeitspotenziale der neuartigen Fertigungsmethoden für den Leichtbau von Faserverbundsystemen? Entdecken Sie die Potenziale von Coreless Filament Winding als neuartigen Ansatz der additiven Fertigung. Direkt zu
- Pavillons als Anwendungsbeispiele von Coreless Filament Winding! Lernen Sie reale Beispiele der Umsetzung neuartiger Planungs- und Fertigungsmethoden für den Leichtbau mit Faserverbundsystemen kennen. Direkt zu
Co-Design-Ansätze für Nachhaltigkeit durch Faserverbundsysteme
Wie Leichtbausysteme allgemein müssen auch Faserverbundsysteme anspruchsvolle funktionelle und technische Anforderungen erfüllen. Gleichzeitig besteht dabei die Herausforderung der Minimierung von Materialeinsatz und Kosten. Co-Design unterstützt Architekt*innen und Planer*innen bei der Reduktion von Materialeinsatz und Kosten.
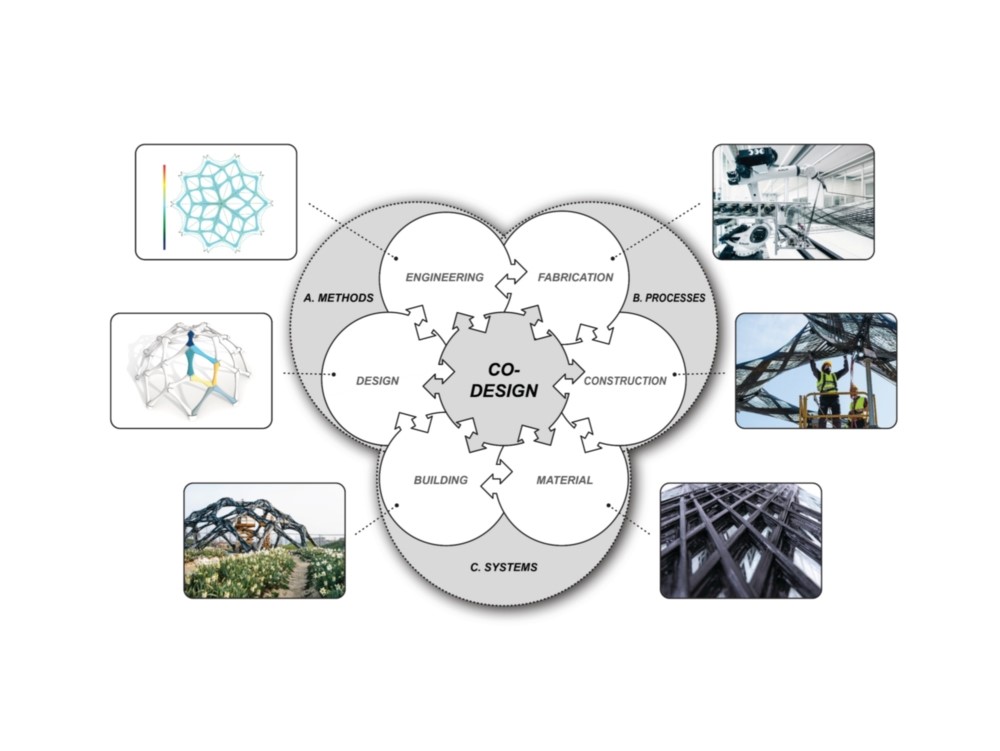
Co-Design integriert die verschiedenen Disziplinen im Produktentwurf von Faserverbundsystemen durch computerbasierte Ansätze für die kontinuierliche Zusammenarbeit interdisziplinärer Teams. Im Ergebnis entstehen neue Möglichkeiten für innovative Lösungen, die anspruchsvolle funktionelle und technische Anforderungen erfüllen und sich mit Hilfe von Robotern hocheffizient fertigen lassen.
Mittels Co-Design, welches die Anforderungen aus Architektur, Tragwerk und robotischer Fertigung berücksichtigt, können die Potenziale von Faserverbundsystemen ideal genutzt werden. Die Dichte und Ausrichtung der Fasern können bauteilspezifisch angepasst werden, sodass im gleichen Zuge auch die Fertigungsbedingungen bedacht sind. Gleichzeitig erfolgt die Gliederung hinsichtlich struktureller Auslegung und architektonischer Aspekte. [Menges et al. 2020]
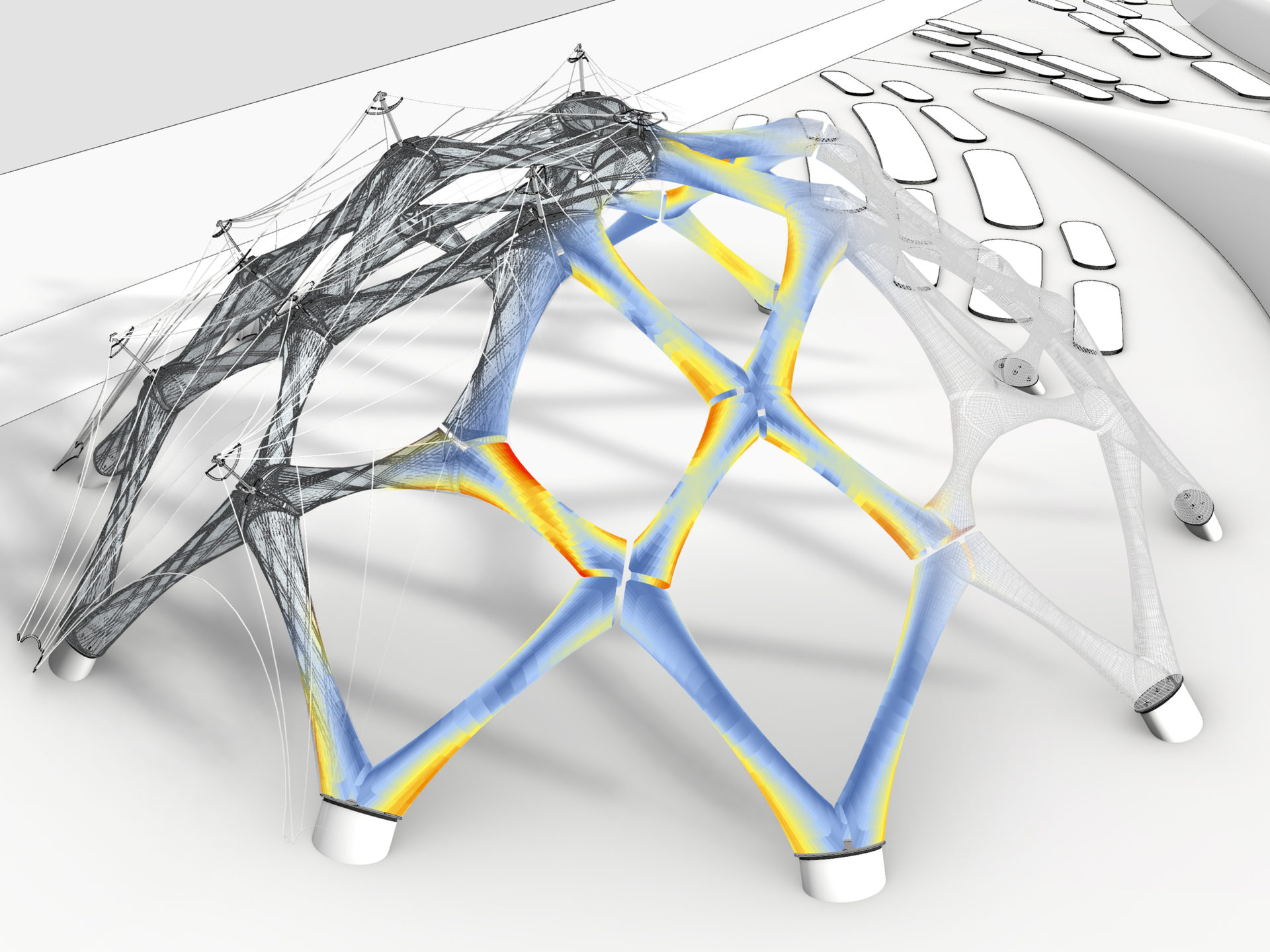
Um das volle Potenzial digitaler Technologien zu nutzen und das Planen und Bauen in einem integrativen und interdisziplinären Ansatz neu zu denken, untersucht das Exzellenzcluster IntCDC Co-Design-Ansätze.
Erleben Sie die Anwendung von Co-Design anhand des BUGA Faserpavillons 2019.
Die CFK-Ökobilanzdatenbank bietet Zugriff auf fundierte Primärdaten zu verschiedenen Herstellungsprozessen im Bereich CFK auch für die Anwendung im Bauwesen.
Nachhaltigkeit durch Einsatz neuer Fertigungsmethoden für Faserverbundsysteme
Zur Umsetzung des durch den Co-Design-Ansatz entwickelten Entwurfs wird mit Coreless Filament Winding ein neuartiger Fertigungsansatz eingesetzt. Beim Coreless Filament Winding werden Bauteile aus Faserverbundkunststoff (FVK) in einem robotergestützten, kernlosen Faserwickelprozess hergestellt. Das Institut für Computerbasiertes Entwerfen und Baufertigung (ICD) und das Institut für Tragkonstruktionen und konstruktives Entwerfen (itke) der Universität Stuttgart haben diesen neuartigen Ansatz zur additiven Fertigung gemeinschaftlich entwickelt.
Hierbei werden Faserrovinge von Robotern frei auf ein Wickelgerüst gelegt. Die resultierende Form ergibt sich aus der Wickelsyntax und der daraus resultierenden Interaktion zwischen den gelegten Fasern. Folglich ist ein aufwendiger Formenbau für die Herstellung eines Wickelkerns nicht erforderlich. [La Magna et al. 2016] [Pérez et al. 2020]
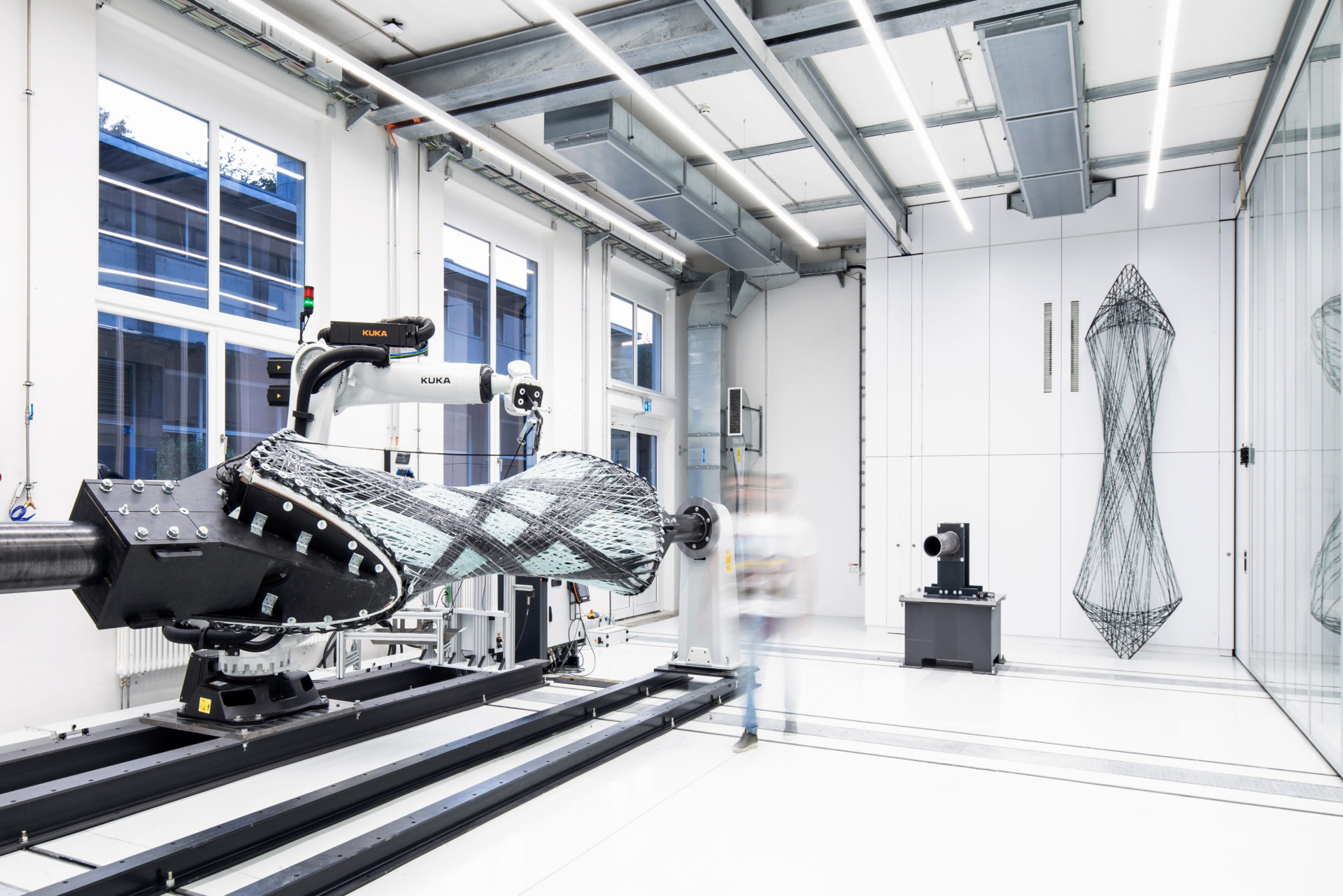
Coreless Filament Winding ermöglicht somit eine maßgeschneiderte Form und individuelle Faserlagen für jedes Bauteil ohne wirtschaftliche Nachteile gegenüber einer Serienfertigung gleicher Bauteile. So sind Bauteile und Konstruktionen von sehr variabler Größe möglich. Gleichzeitig ermöglicht Coreless Filament Winding durch maßgeschneiderte Formen auch sehr komplexe Bauteilgeometrien. Darüber hinaus entstehen keine Produktions- oder Materialabfälle.
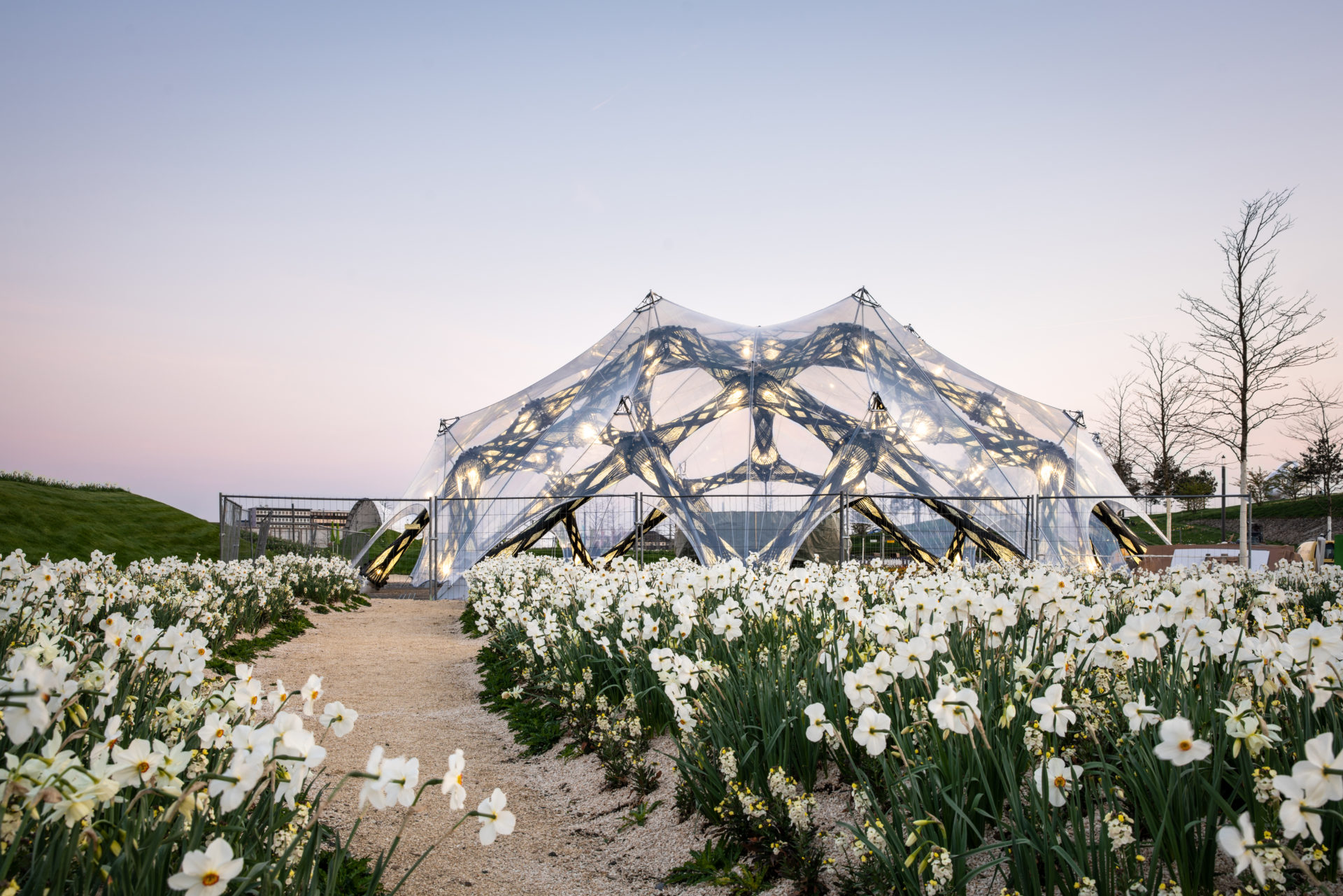
Materialeinsparung bei Bauteilen
Mit dem Faserwickeln zur Herstellung des Pavillons wurde schon von Grund her ein ressourcenschonendes Verfahren gewählt. Die präzise Ablage des Fasermaterials in Kraftrichtung wird durch den robotischen Fertigungsprozess ermöglicht. Die Flexibilität dieser digitalen Fertigungsmethode erlaubt es, jedes Bauteil mit unterschiedlicher Fasermenge und -anordnung zu fertigen. Orientierung, Ausrichtung und Dichte der Fasern sind präzise abgestimmt und lokal ausdifferenziert, so dass nur dort Material platziert wird, wo es tatsächlich benötigt wird. Durch diesen Paradigmenwechsel von standardisierter Serienfertigung identischer Teile hin zur individualisierten und digitalen Vorfertigung lokal angepasster Bauteile ist wesentlich weniger Material notwendig als in üblichen Konstruktionsweisen. [La Magna et al. 2016]
Diese Fertigungsmethode eröffnet also nicht nur neue architektonische und konstruktive Möglichkeiten, sondern bietet vor allem hinsichtlich ihrer Materialeffizienz neue Ansätze für das Bauwesen.
Einsparungen beim Formwork
Ein herausragender Vorteil des roboterunterstützten freien Faserwickelns ist, dass es vollkommen ohne den sonst üblichen material- und kostenintensiven Formenbau auskommt. Somit entfällt ein ressourcen- und energieintensiver Teil der FVK-Fertigung gänzlich.
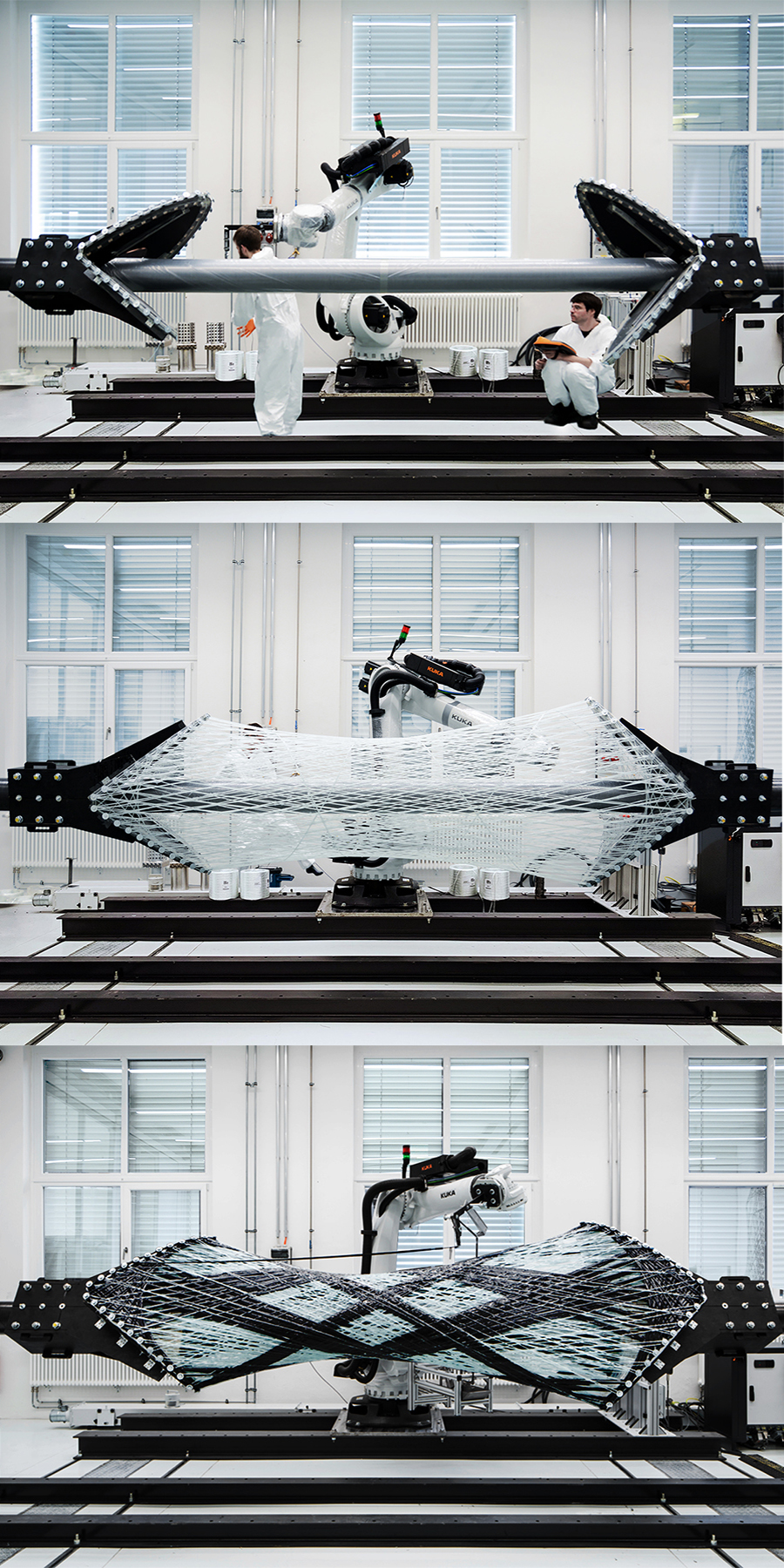
In dem Wickelverfahren werden die Faserbündel nicht auf einer Form oder einem Kern abgelegt, sondern zwischen zwei einfachen und wiederverwendbaren Rahmen frei im Raum gespannt. Dabei werden die Faserbündel individuell und lastgerecht mit einem Roboterarm zwischen diesen minimalen Rahmen gewickelt. Das ausgehärtete Faserverbundmaterial bildet nach Entnahme des Rahmens ein sehr leichtes und zugleich hochleistungsfähiges Bauteil. Mit diesem Ansatz werden die Fasern direkt von der Spule in die Position gebracht, wo ihre Verstärkungswirkung eine maximale Wirkung aufbringt. [Dörstelmann et al. 2014][Parascho et al. 2015][Prado et al. 2017]
Herstellung des BUGA Faserpavillon 2019 © ICD-ITKE Universität Stuttgart
Vermeidung von Abfällen
Bei dieser Fertigungsmethode entfällt ebenfalls jeglicher Verschnittabfall von Fasermaterial, der bei fast allen anderen gängigen Fertigungsmethoden entsteht. So kommt es nicht nur zu einer annähernd 100 Prozent Ausnutzung des Materialpotenzials, sondern es werden auch energieaufwändige Nachbearbeitungen vermieden. Es ist auch nicht notwendig, weder in der Fertigungsvorbereitung noch nach der Fertigung, Fasermaterial durch zerspanende Prozesse zu säumen oder zuzuschneiden. Dadurch wird die Herausforderung der Zerspanung oder des Schneidens von Faserverbundwerkstoffen vermieden. Selbst der eingesetzte Rahmen fällt nicht als Produktionsabfall an, da er zur Fertigung weiterer Bauteil wiederverwendet werden kann. [Dörstelmann et al. 2014][Parascho et al. 2015][Prado et al. 2017]
Einsatz von Naturfasern (in Planung)
Der Einsatz von Naturfasern wie Hanf- oder Flachsfasern ist für die Bauteilproduktion denkbar und könnte die Nachhaltigkeit des Leichtbaus mit Faserverbundsystemen erhöhen. Naturfasern sind jedoch bisher schlechter verarbeitbar und haben geringere Steifigkeiten als Karbonfasern. Hier besteht demnach noch Forschungsbedarf, wie diese Eigenschaften beeinflusst werden können, um die Vorteile der Nachhaltigkeit nachwachsender Rohstoffe zu nutzen. Aktuell werden verschiedene Faserverbundsysteme an einem Demonstrator getestet. Dabei spielt das Harz eine entscheidende Rolle. Das Harz trägt zur Festigkeit bei und hat deshalb einen hohen Gewichtsanteil.
Es wird außerdem parallel der Einsatz von biologischem Harz getestet. Da sich die Projekte jedoch gerade in der Durchführung befinden, liegen derzeit noch keine verwertbaren Daten vor.
Erleben Sie die Anwendung des robotergestützten, kernlosen Faserwickelprozesses anhand des BUGA Faserpavillons 2019 als Serienproduktion.
Wo wurde Coreless Filament Winding bereits eingesetzt?
Die Visualisierung bietet einen Überblick über die Forschungsarbeiten am ICD und itke. Die Kennzahlen von vier Faserpavillons, deren Elemente mit dem innovativen Co-Design-Ansatz und robotergestützten Fertigungsverfahren hergestellt wurden, sind in einem interaktiven Diagramm dargestellt. Entdecken Sie die Eigenschaften und Besonderheiten der einzelnen Pavillons, indem Sie sich die verschiedenen Kennzahlen anzeigen lassen. Beim Klick auf die einzelnen Datenpunkte erhalten Sie außerdem zusätzliche Informationen zu den Hintergründen.
Anwendung des Co-Design-Ansatzes:
© ICD-itke Universität Stuttgart BUGA Faserpavillon 2019 © ICD-itke Universität Stuttgart
Anwendungsbeispiele von Coreless Filament Winding:
© ICD-itke Universität Stuttgart ICD/itke Forschungspavillon 2016-17 © ICD-itke Universität Stuttgart
Bezug zu den Zielen für eine nachhaltige Entwicklung
Durch ihre Nachhaltigkeitspotenziale adressieren neuartige Planungs- und Fertigungsmethoden für Faserverbundsysteme direkt oder indirekt folgende Ziele für eine nachhaltige Entwicklung (Sustainable Development Goals – SDGs). Dieser Bezug basiert auf einer qualitativen Zuordnung der Autor*innen und erhebt keinen Anspruch auf Vollständigkeit.

Wollen Sie mehr erfahren?
Eine Möglichkeit, Faserverbundsysteme ökobilanziell zu betrachten, stellt die CFK-Ökobilanzdatenbank dar. Die Datenbank bietet Industrieunternehmen und Forschungseinrichtungen Zugriff auf fundierte Primärdaten zu verschiedenen Herstellungsprozessen im Bereich CFK. Sie bildet damit eine wichtige Hilfe bei Entscheidungen für Verbesserungen der Produktnachhaltigkeit. Falls Sie Interesse an neuen Methoden zur Verarbeitung von Faserverbundwerkstoffen haben, oder eigene Forschungsfragen diskutieren möchten, melden Sie sich gerne bei einem unserer Ansprechpartner*innen.
Für weitere Informationen zu verschiedensten Themen rund um Nachhaltigkeit von Faserverbundsystemen finden Sie hier eine Weiterleitung auf die Webseite des Fraunhofer IBP. Interessieren Sie sich tiefer für die Themen Co-Design, Coreless Filament Winding oder die Faserpavillons, können Sie über den Link unten auch auf die Webseiten der Institute der Universität Stuttgart itke und ICD springen.